diaphragm seals deburring, turning lines removal and polishing technology method of rubber and plastic product parts
How to deburr,deflash,remove turning lines of rubber, plastic diaphragm seal parts?
The diaphragm seal is a key component of pneumatic pumps and valves, diaphragm pump valve bodies and other products. Its main function is to perform the sealing function. It has been widely used in petrochemical, electric power, aviation, machinery and textile, medical and other industries. The main materials are PTFE polytetrafluoroethylene, Teflon and other polymer materials. There are slight burrs and turning lines in the production process, which will affect the sealing performance of the product. How to mechanically remove burrs and turning lines on the surface and reduce the roughness is a very troublesome problem. In this case, we will share a PTFE sealing diaphragm product high-efficiency deburring, removal of turning lines to reduce the surface roughness of the process technology and method. This finishing process solution is also suitable for deburring, deflashing and polishing of polymer products made of other materials such as polyester and resin.
- jerrylu
- 2024-06-05
- 0 Comments
1. Plastic sealing diaphragm before polishing
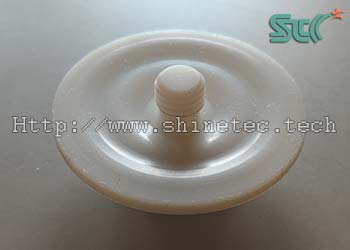
Materials:
PTFE(polytetrafluoroethylene)
Appearance:
surface burrs and turning tool lines
Shape:
circular
Size:
D40*20 mm
Pre-polishing process:
injection molding
Post-polishing process:
packing
2. Finishing and polishing requirements
- deburring, deflashing, removal of turning tool lines.
- smooth surface with a roughness of Ra 0.5 or less.
3. Plastic sealing diaphragm polishing process details:
Polishing processes | (1) deburring, removal of turning tool lines | (2) reduce roughness of fine polishing | (3) drying |
---|---|---|---|
Machine and equipment | plastic parts polishing machine | plastic parts polishing machine | dryer |
Speed | highest | highest | highest |
Abrasive media | heavy cut ceramic deburring media | porcelain polishing media | no |
Abrasive media to workpiece | 4:1 | 6:1 | no |
Chemical compound | cutting liquid | fine polishing liquid | no |
Water | appropriate amount,the liquid level is 30mm above the abrasive media | appropriate amount,the liquid level is 30mm above the abrasive media | no |
Polishing time | 30 minutes | 30 minutes | 5 minutes |
Remark | parts separated and picked up automatically, rinsed with water | parts separated and picked up automatically, rinsed with water | drying |
4. The plastic sealing diaphragm removing turning tool lines after polishing
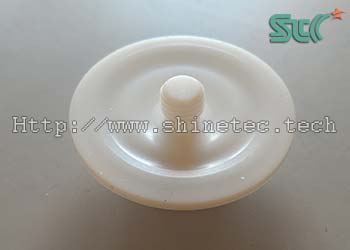
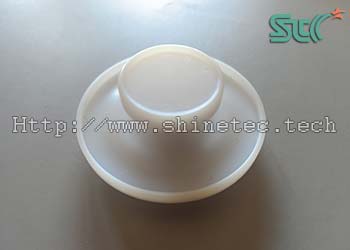
5. Additional instructions
-
The burrs on the surface of the sealing diaphragm are relatively slight, but the turning tool lines are very deep. The rough finishing and polishing machine uses a special polishing machine for plastic products. Rough grinding uses coarse-grained abrasives media to achieve the effect of removing burrs and turning tool marks.
Fine polishing uses precision finishing ceramic media with micro-cutting force and fine-grained tumbling media, which can further reduce the surface roughness. - After fine polishing, use an automatic separating machine to separate the product from the abrasive media, and then use a dryer to dry it after cleaning.
6. Final summary
- In this case, we demonstrate the process solution of automated deburring, removing turning tool lines and polishing of a PTFE polytetrafluoroethylene sealing diaphragm product.
-
If you need professional technical support for the deburring, deflashing, removal of turning tool lines and polishing of PE polyethylene, PA polyamide, PP polypropylene, polytrifluoroethylene, polyvinylidene fluoride and plastic, rubber and other polymer material product parts or the following plastic accessories, you can refer to the above cases:
Plastic product deburring and finishing method
Plastic product deburring tool equipment
How to deal with plastic product burrs
CNC plastic hole bottom burr removal
Injection molded parts deburring
Plastic product deburring
Plastic parts deburring
How to remove plastic burrs
How to grind off burrs on plastic products
Quickly remove burrs from plastic products
Plastic parts deburring process
What is the best polishing method for deburring plastic parts
How to deburr rubber products
What to use for deburring rubber products
How to quickly remove burrs from rubber products
Rubber deburring process
Rubber product polishing process
Rubber product surface polishing
What to use for polishing rubber
How to polish rubber smoothly