Metal material hafnium parts polishing and deburring process technology method
How to automatically and quickly chamfer, deburr and polish small hafnium parts?
Metal materials include carbon steel, general-purpose alloys such as aluminum alloys, stainless steel, zinc alloys, etc.; and high-purity elemental metals, such as gold, silver, copper, aluminum, hafnium, gallium and other metals; high-purity precision alloy materials such as aluminum-copper alloys , molybdenum and niobium alloys, etc.; precious metals & rare metals such as titanium, iridium, tungsten, etc.; and rare earth metals such as cerium, gadolinium, lanthanum, etc., in the shapes of plates, coils, rods, pipes, wires, grain, blocks, ingots, Powder etc. To obtain a satisfactory surface effect, do you know what kind of finishing and polishing process is required for the burrs, flash, and scale produced after metal materials are cast, forged, rolled, drawn, pierced, stamped, sheared, etc. ? In this case, we will share the process solution for chamfering, deburring, and descaling and polishing the surface of metal hafnium parts. This polishing process is also suitable for surface polishing of other hard metal products.
- jerrylu
- 2024-06-03
- 0 Comments
1. Metal hafnium parts before polishing
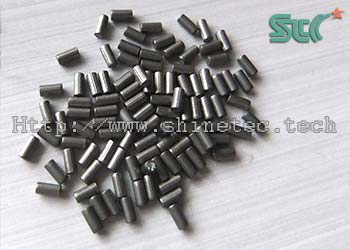
Materials:
metal hafnium
Appearance:
burrs on the cut surface and oxide scale on the surface.
Shape:
cylinder
Size:
2.5*15MM
Pre-polishing process:
sawing
Post polishing process:
packing
2. Requirements for deburring and polishing
- cutting end is chamfered without burrs.
- smooth,brightened surface, no burrs, oxide scale.
3. Details of the polishing process of metal hafnium parts:
Process steps | (1) rough finishing, chamfering, deburring and descaling | (2) fine polishing | (3) drying |
---|---|---|---|
Machine and equipment | centrifugal barrel finisher | centrifugal barrel finisher | centrifugal spin dryer |
Amplitude and speed | high speed | high speed | high speed |
Tumbling media | spherical ceramic deburring media | spherical white corundum finishnig media | no |
Abrasive media to workpiece ratio | 4:1 | 6:1 | no |
Finishing and polishing compound | finishing liquid | polishing liquid | no |
Water | appropriate amount, the liquid level exceeds the abrasive media by 20mm | appropriate amount, the liquid level exceeds the abrasive media by 20mm | no |
Polishing time | 30 minutes | 30 minutes | 15 minutes |
Remark | manual separating and picking up, rinsing with water | manual separating and picking up, rinsing with water | drying, no separating |
4. The effect after polishing of metal hafnium parts
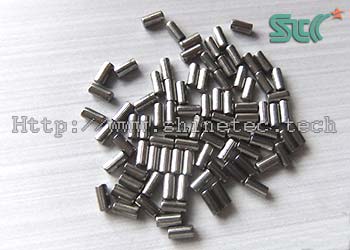
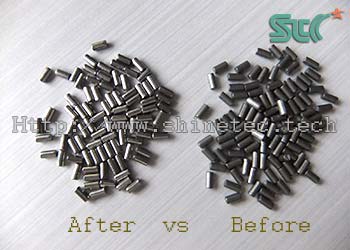
5. Additional instructions
-
Because this hafnium product is a small-sized workpiece with high hardness, it requires strong cutting force to chamfer, deburr and remove scale. Therefore, the rough finishing process is using high-speed centrifugal barrel finishing machine, with heavy cutting force ceramic deburring ball.
The precision finishing and polishing brightness also uses a centrifugal barrel finishing machine, with high hardness and light cutting force white corundum polishing ball to improve surface brightness. - Because the number of products processed is small, product separating can be done manually using screens to reduce equipment purchase costs.
- In order to improve the anti-rust and anti-corrosion performance of the product after being exposed to water, a centrifugal spin dryer used for drying.
6. Final summary
- In this case, we demonstrate a process for surface chamfering, deburring and polishing of parts machined with metallic material – hafnium.
- This process is also suitable for surface polishing of other hard metal material processing parts.