Laser engraving product parts deburring, descaling and mirror polishing process method
How to deburr, descale and mirror-polish parts of laser engraving products?
Laser engraving is an exquisite application of modern precision machining and manufacturing industry. Based on CNC technology, laser beam is used to irradiate the surface of the workpiece, and the material is evaporated, gasified or ablated through instant high temperature to obtain specific patterns. In the industries of advertising decoration, printing and packaging, leather shoes and clothing, model making, craft gifts, etc., laser engraving, a precision machining technology, has been widely used. Today we will share a case of how to remove turning tool pattern, stains, oxide scale and burrs from the camera lens cover of aluminum alloy to achieve mirror polishing. This finishing process solution is also suitable for the deburring, descaling and polishing needs of other precision machining product parts such as laser, plasma, and flame cutting.
- jerrylu
- 2024-06-08
- 0 Comments
1. The laser engraved aluminum alloy camera parts before mirror polishing
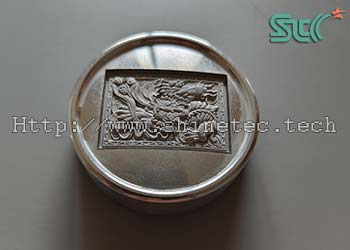
Materials:
aluminum alloy
Appearance:
surface burrs, turning tool lines, oxide scale
Shape:
special-shape
Size:
45*10 MM
Pre-polishing process:
laser engraving
Post-polishing process:
chrome plating
2. Finishing and polishing requirements:
- deburring, removing turning tool lines, descaling, cleaning.
- surface mirror polishing
3. Laser engraving aluminum alloy camera parts mirror polishing process details:
Process steps: | (1) deburring, descaling for rough finishing | (2) reduce roughness for fine finishing | (3) mirror polishing |
---|---|---|---|
Machine and equipment | vibrating finishing machine | vibrating finishing machine | mirror polishing machine |
Speed | highest | highest | highest |
Tumbling Media | angle cut tri-angle ceramic tumbling media | tetrahedron-shaped resin media | mirror polishing media |
Abrasive media to workpiece | 4:1 | 4:1 | 8:1 |
Chemical Compound | finishing compound | polishing compound | polishing paste |
Water | appropriate amount, liquid level does not exceed abrasive media | appropriate amount, liquid level does not exceed abrasive media | no |
Polishing time | 120 minutes | 60 minutes | 180 minutes |
Remark | parts separated and picked up automatically, rinsed with water | parts separated and picked up automatically, rinsed with water | mirror polishing |
4. The laser engraved aluminum alloy camera parts after mirror polishing
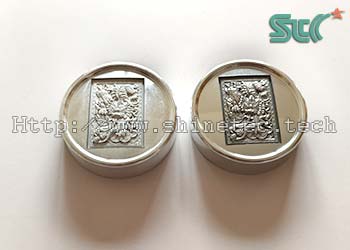
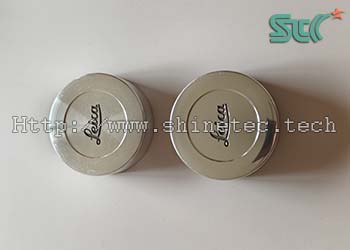
5. Additional instructions
- The laser engraving beam has strong energy, so it will generate very high temperature during engraving, which can easily form a hard and wear-resistant oxide layer on the surface of product parts. In addition, the precision of laser engraving is very high, and the strokes and lines in the pattern are very fine, so it is difficult for abrasive media to penetrate into these parts for finishing. Now we use a vibrating finishing machine, which has strong finishing force and high cutting efficiency, and the working bowl uses an anti-collision divider structure, thus avoiding the problem of collision and damage between workpieces. Abrasive media uses a heavy-cutting angle cut tri-angle ceramic tumbling media, which can achieve the effect of rapid deburring and descaling.
- Fine finishing uses light cutting force tetrahedron-shaped plastic media, also called polyester media. This tumbling media has small grit size and light weight, will not cause deformation of the workpiece, and can further reduce the surface roughness.
- The last step after fine finishing is to use a mirror vibratory bowl polishing machine with precision finishing media to enhance the brightness and mirror polishing.
6. Final summary
- In this case study, we demonstrated the process of automatically removing the burr, oxide scale, turning tool lines from the surface of a laser-engraved aluminum alloy camera component to achieve mirror polishing effect.
-
If you need professional technical support for laser, plasma, wire cutting and other precision hardware parts or the following products in terms of deburring, deburring, removal of turning tool marks, mirror polishing, you can refer to the above cases:
Deburring methods for laser engraving
How to remove burrs from laser engraving
How to deal with burrs from laser engraving
Deburring methods for laser cutting
How long does it take to remove oxide scale from laser engraving
How to remove oxide scale from laser engraving
Laser descaling
Principle of laser descaling
Laser removal of oxide layer
How to adjust parameters for laser cutting with burrs
Why are laser cutting burrs large
How to remove burrs from laser cutting
How to solve burrs in laser cutting
Deslagging methods for laser cutting