Automated finishing and polishing technology for cast iron parts
How to deburr, descale, polish, brighten the cast iron parts?
Items cast from molten iron are collectively called cast iron parts. Due to the influence of the manufacturing process, defects such as pores, pinholes, slag inclusions, cracks, pits, rust spots, burrs, and flash often occur. Do you know how to automatically remove burrs, flash, rust and scale, and polish and brighten cast iron parts? In this case, we will share the process technology and methods of deburring, derusting and descaling, and polishing brightness of an electric hardware used in the power industry – steel foot cast iron parts. This polishing process solution is also applicable to the surface polishing of other hard metal casting parts.
- jerrylu
- 2024-06-03
- 0 Comments
1. Cast iron steel feet before polishing
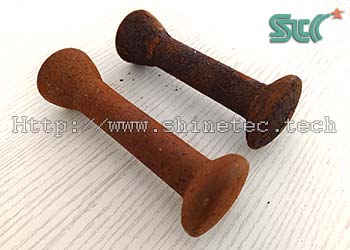
Materials:
cast iron
Appearance:
thick oxide skin on the surface
Shape:
barbell-shaped iron castings
Size:
40*200MM
Pre-polishing process:
rolling
Post-polishing process:
galvanizing
2. Finishing and polishing requirements
- deburring, descaling
- smooth, bright surface, no burrs, no oxide scale
3. Cast iron steel foot polishing process details:
Process steps | (1) rough finishing of deburring, descaling | (2) fine polishing | (3) vibratory dryer |
---|---|---|---|
Machinery and equipment | vibratory finishing machine | vibratory finishing machine | vibratory dryer |
Speed | highest | highest | highest |
Tumbling media | Angle cut cylinder ceramic media | Spherical stainless steel media | corn cob polishing media |
Abrasive media to workpiece ratio | 4:1 | 6:1 | 8:1 |
Finishing and polishing compound | finishing liquid | polishing liquid | no |
Water | appropriate amount,the liquid level does not exceed the tumbling media | appropriate amount,the liquid level does not exceed the tumbling media | no |
Polishing time | 60 minutes | 30 minutes | 15 minutes |
Remark | parts separated and picked up automatically, rinsed with water | parts separated and picked up automatically, rinsed with water | vibratory drying |
4. Cast iron feet after finishing and polishing

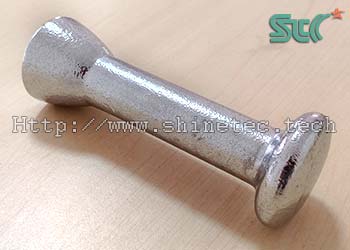
5. Additional instructions
-
Cast iron parts are generally medium-to-large product components, and most of the surface treatments are done by sandblasting and shot blasting. However, this product is small in size and large in quantity, with a daily output of several tons. In order to improve efficiency and surface treatment quality, a vibratory finisher is used with heavy-cutting-force angle cut cylinder tumbling media for rough finishing. The sharp edge of the ceramic media can reach into grooves, corners, and gaps to remove burrs and oxide layers.
For brightening polishing, a general-purpose vibratory polishing machine is used. The polishing media is made of stainless steel ball specially designed for polishing brightness, which can improve the surface brightness and achieve a shiny effect. - In order to improve the anti-rust and anti-corrosion performance of the product after water treatment, it is immersed in a anti-rust liquid for anti-rust treatment after polishing. Finally, a vibrating dryer is used to dry the surface moisture and dry it.
6. Final summary
- In this case, we demonstrated the process of deburring, descaling, derusting, polishing, brightening of a steel foot of cast iron product using a polishing machine.
-
If you need professional technical support for the following polishing issues of cast steel parts, you can refer to the above cases:
Polishing of cast iron parts
How long does it usually take to polish cast iron parts
Methods for deburring cast iron parts
Automation of deburring cast iron parts
Rust removal of cast iron parts
How to remove rust from cast iron
How to remove oxide scale from cast iron parts
What are the methods for removing rust from cast iron parts
How to remove rust from cast iron parts
Polishing of cast iron parts
Polishing of castings
How to polish iron products
Polishing and finishing of cast iron
Polishing process of cast iron
How to remove burrs from iron parts
Descaling of castings
Polishing process of cast iron
What are the methods and techniques for polishing castings
Polishing technology of pig iron
Polishing process of electric hardware