Deburring,descaling, degreasing of stainless steel welded pipe, tube cutting parts, mirror polishing technology
How to remove burrs, oxide scale, degrease and mirror polish stainless steel welded pipe cutting parts?
Stainless steel pipes, tubes can be divided into stainless steel seamless pipes and welded pipes according to the production process. Seamless pipes are produced by perforating, drawing and rolling steel bars, while welded pipes are produced by rolling and welding steel plates. In terms of compressive strength, seamless pipes are better than welded pipes, but the advantages of welded pipes are low cost, simple process and high production efficiency. Today we will share a case of mirror finishing and polishing of a small round tube after sawing from a 304 stainless steel welded pipe, tube. This polishing process solution is also suitable for other hardware parts made of materials such as 201, 316, 321 or nickel-titanium alloys, which require deburring, deflashing, descaling and mirror polishing after sawing, plasma, water jet, electric spark and other cutting processes.
- jerrylu
- 2024-06-13
- 0 Comments
1. The stainless steel welded pipe(tube) cutting parts before polishing
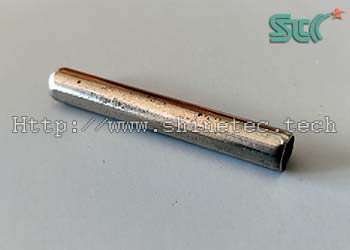
Materials:
304 stainless steel
Appearance:
surface burrs, oil stain, seam
Shape:
round tube
尺寸:
Ø8*50 MM
Pre-polishing process:
sawing
Post-polishing process:
electroplating
2. Finishing and polishing requirements
- deburring, descaling of welded seam
- mirror polishing
3. Polishing process details of stainless steel welded pipe, tube cutting parts:
Process steps: | (1) deburring, descaling for rough finishing | (2) reduce roughness for fine finishing | (3) mirror polishing |
---|---|---|---|
Machine and equipment | vibratory bowl finishing machine | vibratory bowl finishing machine | mirror polishing machine |
Speed | highest | highest | highest |
Tumbling media | spherical deburring ceramic media | fine finishing media | mirror polishing media |
Abrasive media to workpiece | 4:1 | 6:1 | 8:1 |
Chemical compound | finishing compound | polishing compound | polishing paste |
Water | appropriate amount, liquid level does not exceed abrasive media | appropriate amount, liquid level does not exceed abrasive media | no |
Polishing time | 120 minutes | 60 minutes | 180 minutes |
Remark | parts separated and picked up automatically, rinsed with water | parts separated and picked up automatically, rinsed with water | mirror polishing |
4. The stainless steel welded pipe(tube) cutting parts after polishing
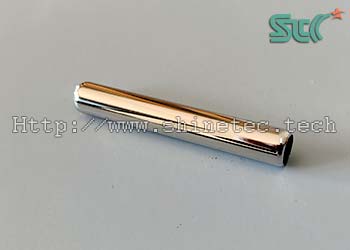
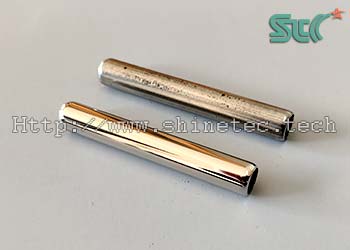
5. Additional instructions
- This stainless steel welded pipe, tube cutting hardware parts product is a small product made by sawing the welded tube. There are obvious burrs on both ends of the pipe, tube, but the tube wall is thin, which can easily cause deformation of the workpiece during polishing. Therefore, the rough finishing and polishing machine uses a vibratory bowl polishing machine with moderate finishing force and high cutting efficiency. The rough finishing uses heavy-cutting spherical ceramic deburring media, which can quickly remove burrs, scales and oil stains.
- Fine finishing uses precision finishing media with light cutting force and small abrasive grain size to further reduce surface roughness.
- The last step after fine finishing is to use a mirror polisher and mirror polishing media to enhance the brightness and mirror polishing.
6. Final summary
- In this case, we demonstrated the process of automated deburring, degreasing, mirror polishing of the outer surface of a 304 stainless steel welded pipe, tube cutting hardware part.
-
If you need professional technical support for deburring, finishing and polishing of stainless steel, nickel-titanium alloy, cemented carbide and other precision hardware parts, cut parts, processed parts, finished products or the following products using sawing, plasma, water jet, electric spark and other processes, you can refer to the above cases:
Stainless steel mirror polishing method
Stainless steel mirror polishing machine
Stainless steel mirror polishing process
How to polish stainless steel to a mirror effect
The best way to deburr stainless steel
How to deal with stainless steel burrs
Stainless steel hole burr removal
What to use to cut stainless steel without burrs
How to deal with burrs on stainless steel laser cutting
How to deburr stainless steel pipes, tubes
What to use to deburr stainless steel pipes, tubes
How to deburr stainless steel welded pipes, tubes
How to deal with stainless steel welded pipes, tubes
How to remove burrs from stainless steel pipes, tubes
How to deburr small stainless steel parts
How to cut stainless steel pipes without burrs
Stainless steel pipe, tube cutting method