How to remove burrs, oxide scale, and mirror-polish titanium alloy precision hardware parts?
Titanium alloy precision hardware parts deburring, descaling, finishing and mirror polishing process technology method
Titanium alloys are widely used in the medical, photographic equipment, glasses, sports, aviation, military and other industries. Titanium alloy materials are also used in the manufacturing of watch cases and watch strap parts due to their excellent properties such as corrosion resistance, light weight, non-allergenic, slow heat transfer (not freezing cold in winter). The traditional polishing process for the surface treatment process in the manufacturing process is to use a manual emery wheel for mirror polishing. In this case, we will share a titanium alloy watch strap part deburring, descaling, mirror polishing and brightening process technology and methods in high-efficiency . This mass finishing process solution is also applicable to deburr, descale, derust, chamfer and mirror polish other materials such as steel, stainless steel, alloy steel and other precision hardware product parts or titanium alloy surgical instruments, medical devices such as artificial joints, bone plates, screws, cardiovascular stents, dental implants and other processed parts.
- jerrylu
- 2024-06-13
- 0 Comments
1. The Titanium alloy watch strap before polishing
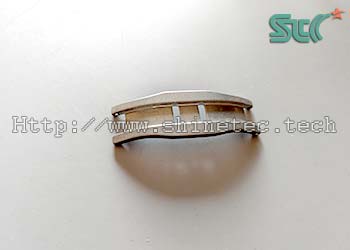
Materials:
titanium alloy
Appearance:
oxide scale, burrs on surface
Shape:
special-shaped
Size:
15*40 MM
Pre-polishing process:
stamping
Post-polishing process:
electroplating
2. Finishing and polishing requirements
- deburring,descaling
- smooth, mirror polishing surface
3. Details of polishing process for titanium alloy watch strap parts:
Process steps | (1) deburring,descaling of rough finishing | (2) reduce roughness of fine finishing | (3) mirror polishing |
---|---|---|---|
Machine and equipment | vibratory finishing machine | vibratory finishing machine | mirror polishing machine |
Speed | highest | highest | highest |
Abrasive media | angle cut tri-angle silicon carbide ceramic media | cone polyester media | mirror polishing media |
Abrasive media to workpiece | 4:1 | 6:1 | 8:1 |
Chemical compound | finishing compound | polishing compound | polishing paste |
Water | appropriate amount, liquid level does not exceed abrasive | appropriate amount, liquid level does not exceed abrasive | no |
polishing time | 120 minutes | 60 minutes | 120 minutes |
Remark | parts separated and picked up automatically, rinsed with water | parts separated and picked up automatically, rinsed with water | high speed mirror polishing |
4. The Titanium alloy watch strap parts after mirror polishing
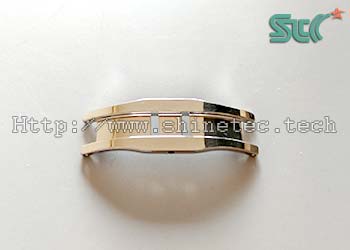
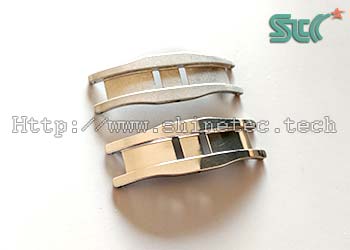
5. Additional instructions
-
In order to improve the batch processing capacity, the rough finishing and polishing machine adopts a vibratory polishing machine, and the batch processing capacity can reach tens or even hundreds of kilograms. Titanium alloy has high hardness, so the heavy finishing uses silicon carbide ceramic media with higher cutting force than heavy-cut brown corundum deburring media, which can achieve the effect of quickly removing burrs and oxide layers.
Fine finishing uses light-cutting precision tumbling abrasive media, cone-shaped plastic media with fine abrasive grit to further reduce surface roughness. - After fine finishing, use a mirror polisher and mirror polishing material to enhance the brightness and mirror polishing effect.
6. Final summary
- In this case, we demonstrated the process solution of automated deburring and descaling of the outer surface of a titanium alloy watch strap component to achieve mirror polishing.
-
If you need professional technical support for deburring and mirror polishing of precision hardware parts such as carbon steel, stainless steel, alloy steel watch straps or cases, or the following titanium alloy parts, you can refer to the above cases:
The best method for deburring titanium alloy
The method for deburring and polishing titanium alloy
How to remove burrs from titanium alloy
Rust removal from titanium alloy
How to finish and polish titanium alloy
Mirror polishing of titanium alloy
The method for polishing titanium alloy
What abrasive media are good for polishing titanium alloy
How to deal with scratches on the surface of titanium alloy
Polishing of titanium alloy surface
How to polish titanium metal
What to use to polish titanium alloy