Non-standard stainless steel wire forming special-shaped spring chamfering, deburring and polishing solution
How to polish non-standard stainless steel wire formed special-shaped springs?
Stainless steel wire formed special-shaped springs are used in product spare parts and instrument components in the chemical, valve, petroleum, and electric power industries, such as motor brushes, switches, video cameras, and computer accessories. This type of precision spring requires both high strength and a smooth and bright surface. So do you know what kind of finishing and polishing process this stainless steel product undergoes to obtain a satisfactory surface effect? In this case, we will share a polishing process for chamfering and deburring the surface of a non-standard stainless steel wire-formed special-shaped spring. This polishing process is also suitable for surface polishing of compression springs, torsion springs, tension springs, clasp springs, medical springs, special-shaped rods, special-shaped springs and other products.
- jerrylu
- 2024-06-03
- 0 Comments
1. Stainless steel wire formed special-shaped springs and buckles before polishing

Materials:
stainless steel
Appearance:
oxide scale and burrs on surface,dark gray.
Shape:
simple curve.
Size:
Ø3*10MM
Pre-polishing process:
cut to shape
Post polishing process:
finished product inspection
2. Requirement for polishing
- smooth surface, no burrs and scale.
- reduce surface roughness, increase gloss, and improve brightness.
- close to mirror polishing effect.
3. Details of stainless steel wire forming special-shaped spring and buckle polishing process
Process steps | (1) Coarse finishing to remove burrs and scale | (2) Fine polishing | (3) Mirror polishing |
---|---|---|---|
Machine and equipment | vibrating bowl finishing machine | vibrating bowl finishing machine | tumbling barrel finishing machine |
Amplitude and speed | highest amplitude,full speed | highest amplitude,full speed | highest amplitude,full speed |
Tumbling media | spherical ceramic deburring media | stainless steel ball | walnut shell polishing media |
Abrasive media to workpiece ratio | 4:1 | 6:1 | 8:1 |
Finishing compound | finishing liquid | polishing liquid | no |
Water | appropriate amount, the liquid level should not exceed the tumbling media | appropriate amount, the liquid level should not exceed the tumbling media | polishing paste |
Polishing time | 1 hour | 30 minutes | 6 hours |
Remark | pick up by hand and rinse with water | pick up by hand and rinse with water | mirror polishing |
4. The effect of stainless steel wire forming special-shaped springs and buckles after finishing and polishing
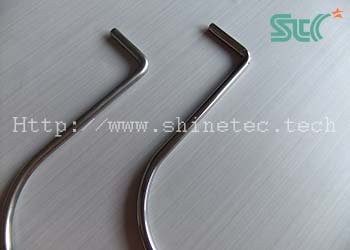
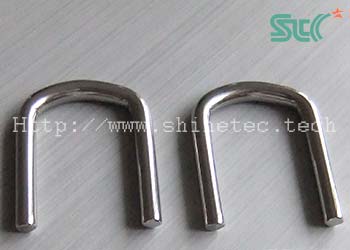
5. Additional instructions
- Because stainless steel is harder material, ceramic deburring ball is used for rough finishing to remove scale and burrs. If you use angle cut triangle ceramic deburring media or angle cut cylinder ceramic deburring media with sharp corners or edges will cause scratches, pitting and other problems on the surface of the product.
- The workpiece material is hard and has no edges and corners, so it can be automatically separated by a machine. There will be no surface damage caused by collision with each other, which greatly improves the efficiency of discharging materials.
-
For stainless steel product parts, polish with stainless steel polishing ball is very effective in brightening. The surface of the product after rough finishing has no luster, but it will become bright after vibratory fine finishing and polishing with stainless steel media.
In order to further improve the smoothness and brightness of the product surface, finally use tumbling barrel polishing machine, combined with walnut shell polishing media, achieves a quasi-mirror polishing effect with the support of polishing paste.
6. Final summary
- In this case, we demonstrate a process of deburring, descaling and brightening for the surface of stainless steel wire-formed special-shaped springs using ceramic deburring media, stainless steel polishing media and mirror polishing media.
- This process is also suitable for surface polishing of compression springs, torsion springs, tension springs, buckle springs, medical springs, special-shaped rods, special-shaped springs, precision buckles and other products.